Packaging Machine Repair Service: Avoid Pricey Break Downs with Specialist Help
Packaging Machine Repair Service: Avoid Pricey Break Downs with Specialist Help
Blog Article
Understanding the Secret Parts and Repair Service Strategies for Packaging Device Upkeep
Effective maintenance of product packaging makers depends upon an extensive understanding of their essential components, consisting of the framework, drive system, and securing devices. Identifying usual upkeep problems, paired with the execution of preventative strategies and fixing methods, can significantly enhance equipment reliability. Furthermore, the choice of repair practices, including making use of OEM components and the relevance of licensed professionals, plays a vital duty in lessening downtime. To truly comprehend the intricacies of these systems and their upkeep, one must take into consideration the more comprehensive implications of neglecting these vital methods.
Key Components of Packaging Makers
Product packaging devices include numerous key components that collaborate to guarantee effective and efficient product packaging procedures. At the core of these machines is the frame, which offers structural integrity and houses the different operating components. The drive system, frequently a combination of motors and gears, facilitates the motion of components, enabling accurate operation throughout the packaging cycle.
Another essential part is the conveyor system, which transports products through various stages of the product packaging process. This is typically enhanced by sensors and controls that keep track of the setting and rate of things, making sure synchronization and lessening mistakes. The filling system is critical for precisely dispensing the best amount of product into packages, whether in fluid, powder, or strong kind.
Securing systems, including warmth sealers or adhesive applicators, play a vital duty in securing bundles, stopping contamination and prolonging life span. Additionally, labeling systems are essential for giving necessary item information, making certain compliance with regulations. The control panel, furnished with easy to use user interfaces, enables drivers to manage equipment functions, screen efficiency, and make modifications as needed, making certain ideal efficiency and efficiency in product packaging procedures.
Typical Maintenance Issues
Reliable procedure of packaging devices relies heavily on routine upkeep to avoid usual issues that can interfere with production. Among these issues, mechanical wear and tear prevails, particularly in components like conveyors, seals, and motors, which can bring about unforeseen downtimes. Additionally, misalignment of parts can cause inefficient operation, triggering items to be incorrectly packaged or damaged throughout the procedure.
One more common maintenance issue involves the buildup of dirt and debris, which can conflict with the equipment's sensing units and relocating parts. packaging machine repair service. This not only affects efficiency but can also pose security dangers. Furthermore, lubrication failures can bring about increased rubbing, resulting in overheating and eventual part failing.
Electrical troubles, typically coming from loosened links or worn-out circuitry, can disrupt equipment functions, causing significant manufacturing delays. Software glitches due to outdated programs or improper setups can prevent the equipment's operation, demanding instant treatment. Addressing these common maintenance problems proactively is essential for ensuring optimal performance and long life of product packaging equipment.
Preventative Maintenance Strategies
Applying preventative upkeep approaches is vital for maintaining the performance and dependability of product packaging equipments. These approaches incorporate a systematic method to maintenance, focusing on the regular evaluation and maintenance of equipment to preempt prospective failures. By sticking to an arranged maintenance program, operators can recognize deterioration on components before they bring about substantial breakdowns.
Key elements of a preventative upkeep method consist of regular inspections, lubrication, element, and cleaning substitutes based on supplier referrals. Using checklists can improve this process, ensuring that no crucial jobs are neglected. Furthermore, keeping precise documents of upkeep activities aids in tracking the equipment's efficiency in time, assisting in notified decision-making concerning future maintenance demands.
Educating staff on the significance of preventative upkeep improves compliance and promotes a Continued society of positive care. Executing a predictive upkeep element, using information analytics and sensing unit technology, can further optimize equipment efficiency by anticipating failings before they take place.
Troubleshooting Techniques
When encountered with breakdowns or inadequacies in packaging machines, using systematic troubleshooting strategies is vital for identifying and solving concerns promptly. The initial step in effective troubleshooting is to develop a clear understanding of the equipment's operational specifications and performance metrics. This entails examining the equipment's specifications, along with any mistake informs or codes shown.
Following, drivers must perform a visual examination, examining for apparent indications of wear, damages, or imbalance. This often includes checking out gears, belts, and sensors to identify possible reasons of breakdown. Gathering functional data, such as production prices and downtime logs, can also supply insights right into repeating problems.
Once potential issues are recognized, using a logical approach to separate the origin is crucial. This might call for testing private parts or systems in a regulated fashion. Involving in conversations with drivers who connect with the machinery regularly can generate useful responses about unusual actions or patterns.
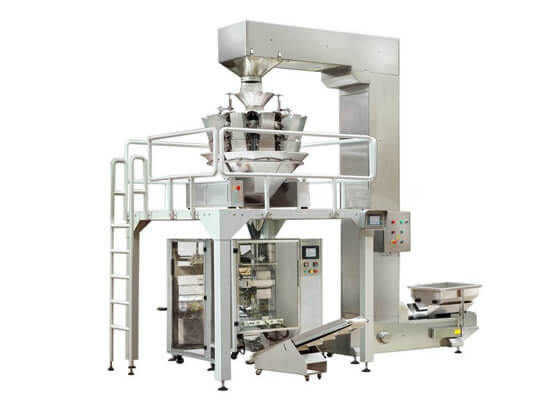
Repair Service and Replacement Best Practices
A detailed understanding of repair service and substitute ideal practices is essential for keeping the longevity and effectiveness of packaging makers. Consistently examining the problem of equipment elements permits prompt intervention, stopping more substantial issues that can cause expensive downtimes.
When repairs are necessary, it is necessary to utilize OEM (Original my site Equipment Maker) parts to ensure compatibility and efficiency. This not only protects the honesty of the machine but also promotes guarantee contracts. In addition, it is recommended to keep an inventory of vital extra parts to view it now facilitate fast substitutes and lessen operational interruptions.
For complex repair work, involving qualified specialists with specialized training in packaging machinery is suggested. They possess the proficiency to identify issues precisely and perform fixings effectively. Furthermore, recording all repair service activities and components replacements is important for preserving a comprehensive upkeep background, which can help in future troubleshooting.
Finally, implementing a proactive technique, including normal evaluations and anticipating maintenance methods, enhances the integrity of product packaging equipments. By adhering to these ideal methods, companies can make sure optimal machine efficiency, lower functional risks, and expand devices life-span.
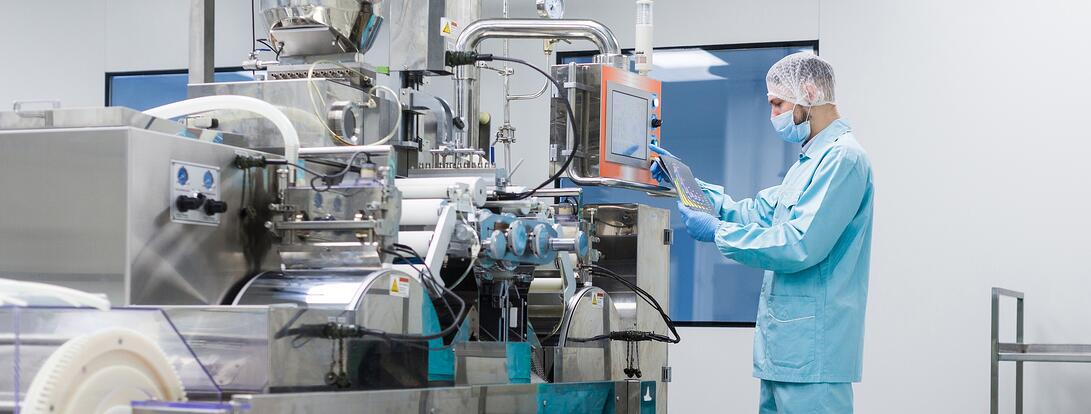
Final Thought
Finally, a comprehensive understanding of packaging maker elements and reliable maintenance approaches is essential for optimal performance. Regular examinations and the usage of OEM parts can substantially reduce downtime, while a well-documented maintenance history promotes proactive care. Utilizing licensed professionals better enhances repair service high quality and dependability. By carrying out these methods, companies can make sure the longevity and efficiency of packaging devices, ultimately adding to boosted operational productivity and lowered costs.
Effective maintenance of packaging equipments pivots on a detailed understanding of their vital parts, consisting of the framework, drive system, and securing devices.Efficient procedure of product packaging equipments depends greatly on regular upkeep to stop common concerns that can interrupt manufacturing.Implementing preventative maintenance methods is important for sustaining the efficiency and dependability of packaging machines. In addition, preserving exact records of maintenance activities help in tracking the device's performance over time, helping with educated decision-making pertaining to future maintenance requirements.
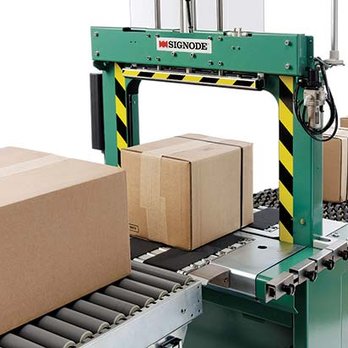
Report this page